KEEL
Problem: keel had many rust blisters (~100 per side) -
mostly about 1/4-1/2" in diameter. Some of the bigger blisters
had broken through the antifouling, exposing rusted steel.
Solution
The best sources of information
about products and procedures were marine paint suppliers' web
pages, as well as on-line forums, and do-it-yourself reports such
as posted on Kelly's F235 site.
I
didn't want to hassle with sand-blasting (although, if done right,
it would probably be easiest and quickest), and decided to grind
off the rust with coarse sand paper. After unsuccessful attempts
with wire brush grinders (too feeble) or disks of sand paper (too
slow) on my electric drill, I ended up mostly using an electric
belt sander with belts of 36-grit paper. I used two belts per
side and finished off with disks of the same paper on my drill
to get at the corners the belt sander didn't reach. I even had
to hand-sand small areas in tight corners and in some depressions
where the keel was not fair. I did not manage to get all the way
to gray metal all over because sand paper couldn't access (i)
small pits created by rust or (ii) old paint that was applied
apparently over a very poorly faired keel and remained in depressions
and pits. I guess I got to gray metal over about 90% of surface.
I applied a powerful paint stripper (Peel Away) to the pits and
depressions, which removed all remaining paint, but not some of
the rust in some of the pits - oh well! I hand-sanded the keel
with 80-grit paper, then wiped off the dust with dry clean rags
immediately before the solvent wash step (below).
I
planned to use InterProtect 2000 (IP2000) epoxy barrier coat
on the hull and the keel (after stripping off all old paint),
which called for the cleaned surface to be washed with a preparative
solvent (thinner 216) before applying the barrier coat. A phone
call to International Paints tech service confirmed that the same
solvent could be used to prep the gray-metal keel and the stripped
hull. I used a new (cheap) bristle brush to wash the keel liberally
with 216. I prepared my first quart of IP2000, which had finished
'activating' by the time the 216 had evaporated. I applied IP2000
rather heavily using a 7" roller and a West System solvent-resistant
closed-cell foam sleeve (sold in pairs at marine stores). I could
apply sequential coats every ~3-4 hours as the weather was warm,
with a light breeze.
I followed the manufacturer's directions
regarding the amount of product needed to give the proper barrier
thickness. If small hull blisters or keel rust bubbles arise in
the future, it'll be a simple matter to sand a very small area
back to the base material, fair if necessary, and recover the
repair with a few coats of IP2000, and some antifouling.
InterProtect 2000 tips
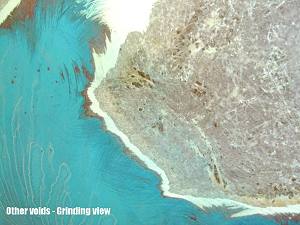
(i) The gray base material (big can) settles considerably,
and can't be mix up well enough just by just shaking the can before
opening it. Instead, use a very stout mixing stick to thoroughly
mix the gray base material before adding the epoxy hardener (small
can) - it's a lot harder to bring up the settled base material
after adding the hardener because the big can is almost completely
full.
(ii) It might be tempting to buy the much
more economical one-gallon IP2000 'kit'. However, even if coating
the entire underwater part of a 24-footer, it provides at least
three heavy coats of coverage, which cannot always be applied
in one day. If left overnight after combining the two parts, IP2000
thickens significantly, and will be hard to apply evenly the next
day.
(iii) If applied carefully using a roller,
IP2000 doesn't run, bit if it's applied too heavily (perhaps to
reduce the number of separate coats), runs can form, which will
be hard to sand out later.
HULL
Problem: underwater part of hull had eight large fiberglass
blisters, 4-6" in diameter.
Solution:
I searched the Internet with key words like "fiberglass blisters",
"gel coat blisters" and "blister repair",
and found lots of useful resources - especially useful was:
Hull Blisters: David Pascoe - Marine
Surveyor
http://www.yachtsurvey.com/blisters.htm
I used a hand drill to puncture the center
of each blister, being careful to avoid the spurt of nasty pale
brown acidic fluid that spurted out. The drill bit only needs
to penetrate the gel coat (~1/8" thick) to release the fluid.
Wear eye protection and waterproof gloves, and wash off any of
the liquid that gets on skin. An electric drill presents an electrocution
risk when the fluid spurts out, and a hammer and screw driver
or chisel could spatter the fluid. I added a few extra holes to
each blister, especially at the lowest point on each, and let
them drain overnight (for my convenience mainly). I used and electric
drill fitted with 4-5" sandpaper disks (36-grit) on a rubber
support to carefully grind out the gel coat and underlying wet
fiberglass mat from each blister, being sure to extend a little
into the surrounding and underlying good material, but not to
grind too deeply in any one spot. I started with a battery-powered
drill, but it didn't have enough power or battery life for the
job. Finer sandpaper clogs and wears out too fast, and coarser
paper is hard to control and risks deep gouges. I created a smooth
transition from the surrounding good gel coat down into the repair
so I could see easily when all the wet material was gone. It was
not necessary to go deeper than about 1/4-1/3" into the hull
to get all the wet glass out, but I had to go at least 1"
outwards in all directions from the initial blister boundary to
get all of the surrounding wet glass out. Under some blisters
I could see obvious voids in the lay-up, which probably promoted
blister formation. Some voids were rather deep so I just cleaned
and dried them thoroughly instead of grinding too deeply into
the hull to remove them.
I
washed the open blister areas with lots of water and let them
dry for a long time (the literature recommends many MONTHS!).
During this time, erect covers to prevent rail and water running
down from the toerails from getting into the repair areas. When
they are very dry (a last-minute dose of hot air from a hairdryer
might help), wash with acetone and fill with new fiberglass mat.
Cut pieces
of woven mat (not chopped-strand mat) to fit the inner 3/4 of
each area: number the areas and corresponding mat pieces if doing
more than one blister. Prepare about 3/4 of a cup of West System
epoxy (no fillers) for each 6-8" repair area, and use a cheap
brush to paint it over all of each repair area. Submerge the piece
of glass cloth into the remaining epoxy until it's fully saturated
(almost transparent), then lay it into the repair area. Note:
if you use too much epoxy to pre-wet the area or the cloth, the
cloth might slide down the hull (on more vertical areas) or the
epoxy will run down onto the surrounding good gel coat, which
will be really hard to sand off later. Use acetone on a paper
towel to wipe excess epoxy from around the repair, but not in
the repair area, and to reposition the mat before it sets so it
doesn't stand proud of the repair. As soon as the epoxy is no
longer tacky, another layer of fresh epoxy can be brushed in,
and overlayed with more cloth. Again, make sure all of the glass
cloth lies below the level of the surrounding gel coat, and that
the cloth is completely impregnated with epoxy. Several fairing
materials can be used (InterLux sells a product for exactly this
application). I faired with two applications of West epoxy mixed
with filler. The first layer had a hard filler in it, and I made
sure it didn't stand proud of the hull when set to avoid having
to sand it. The second/final fairing used the 'softest' West filler,
which I allowed to set slightly proud of the surrounding hull
- I was very careful not to leave and grooves, and as few high
ridges as possible, as this stuff is still pretty hard to sand.
I faired each slight 'bump' by hand-sanding with a long (~8")
sanding block and 80-grit paper.
For a perfect finish, one could leave
the repair areas rough and below flush with the hull, then cover
with a nice layer of new gel coat, but this is not necessary if
a good barrier coat will be added.
NOTE: For more Blister Fix and Bottom Paint comments by
Neil with more detail, please head to the Beneteau
First 235 General Forum for the thread:
Fiberglass
Repair: Blisters
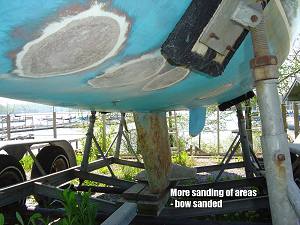
